About us
Individual. Personal. Global.
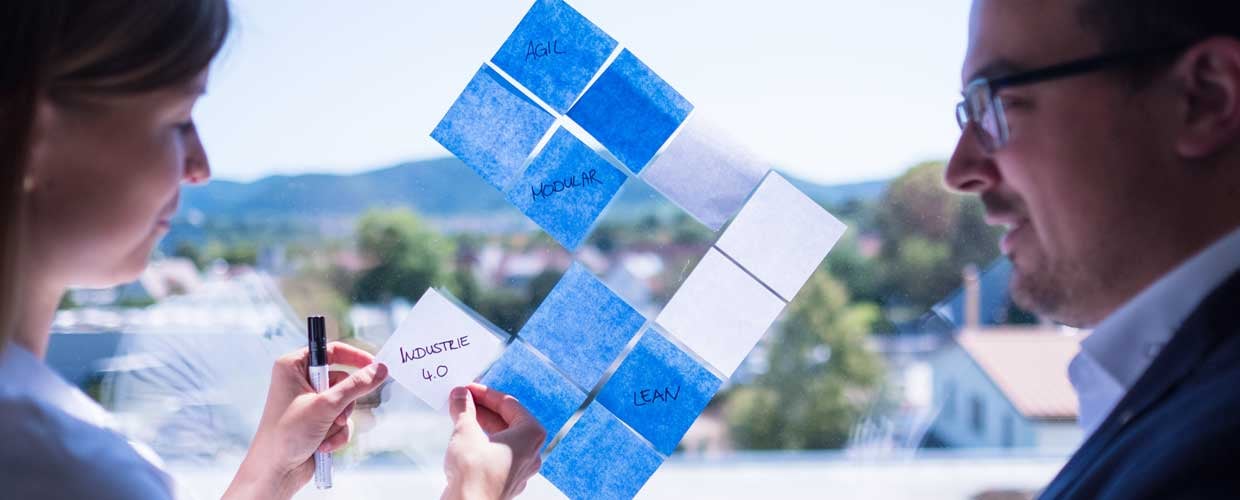
Who we are
The BeeWaTec Group, headquartered in the Swabian town of Pfullingen, Germany, is internationally connected with a flexible and innovative product portfolio around lean manufacturing, agile production, and Industry 4.0, and has a decentralised presence through its own subsidiaries. The family-owned company is the supplier and process partner for many leading European companies in the field of workplace, logistics and production design.
We cannot and will not hide our Swabian roots. This includes the tinkerer and thinker gene as well as the proverbial efficiency thinking, which today benefits customers all over the world when it comes to developing lean, effective, and thus cost-saving solutions.
With our innovative modular system for lean manufacturing, we are one of the leading providers of lean and material flow solutions. We are a system provider and create both stand-alone solutions and complete concepts with integrated solutions for you.
As a medium-sized company, we focus on continuously high-quality standards - this applies to the manufacturing of our products as well as to the application of these systems for our customers.
If you are looking for solutions for a flexible and economical working and production environment, BeeWaTec is your perfect partner.
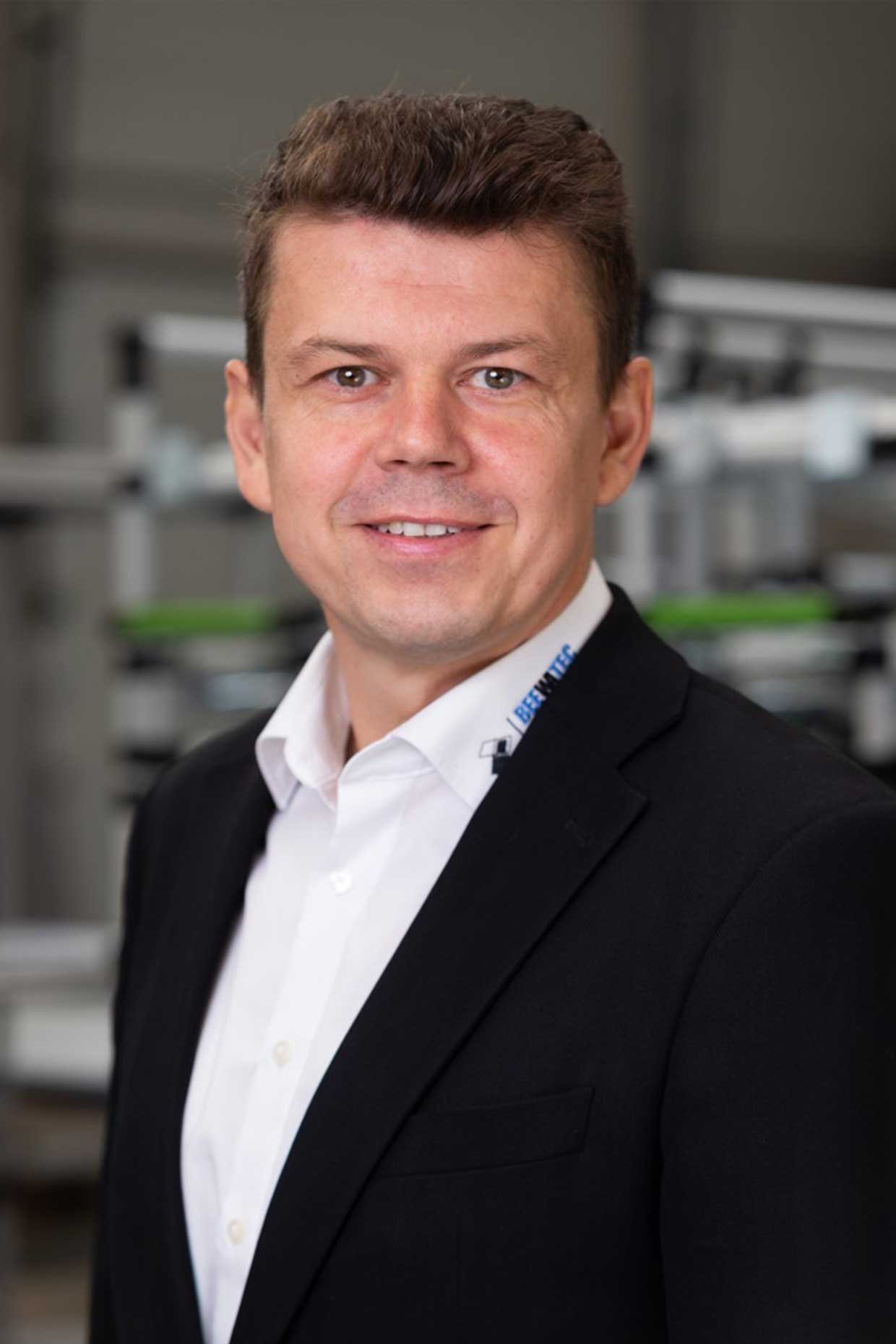
Tomáš Kožoušek
CEO - BeeWaTec Czech
As CEO of BeeWaTec s.r.o., Tomáš Kožoušek is responsible for the strategic and operational orientation of BeeWaTec in the Czech Republic and Slovakia.
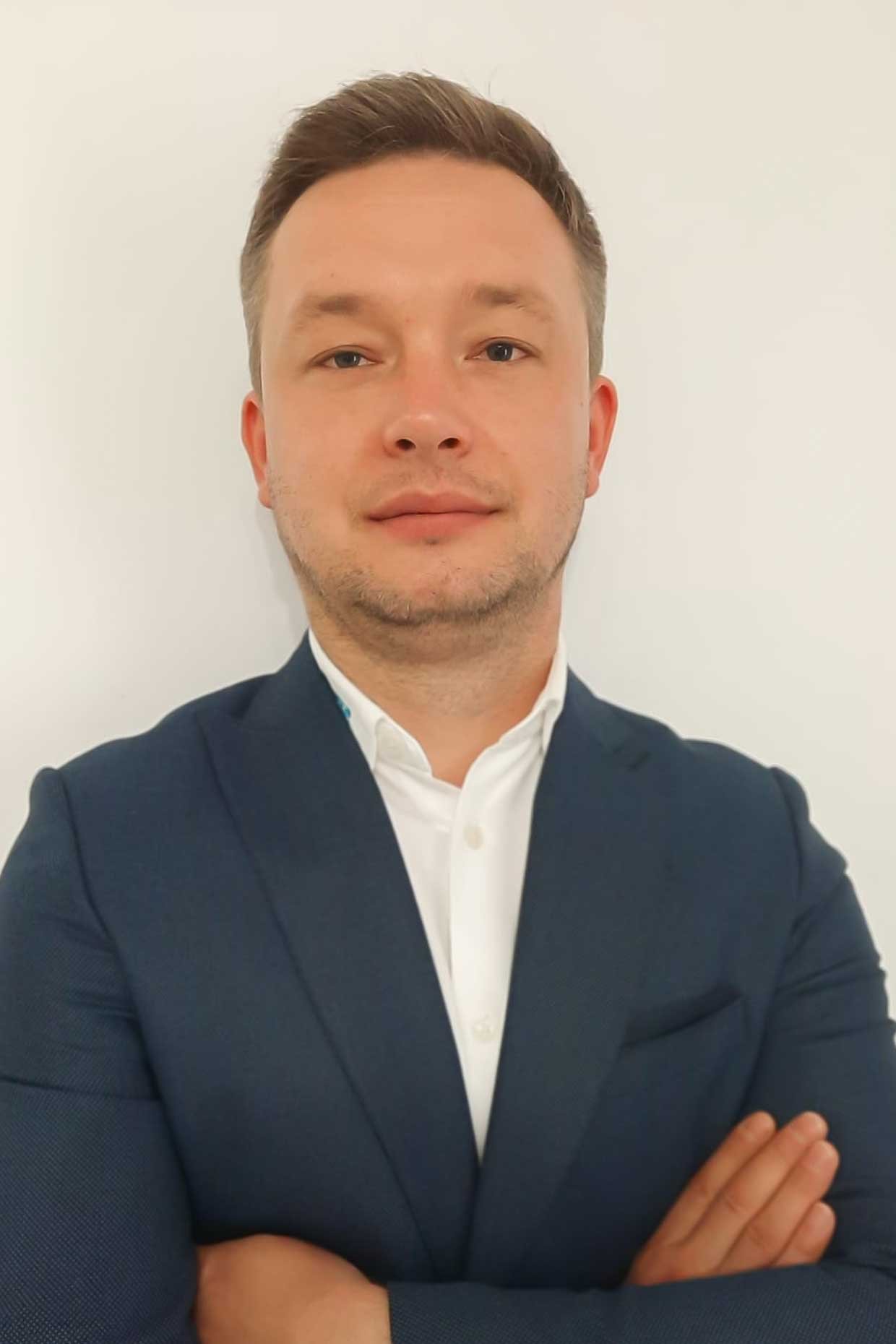
Mark Marton
CEO - BeeWaTec Romania
As CEO of BeeWaTec EastTrade S.R.L., Mark Marton is responsible for the strategic and operational orientation of BeeWaTec in Romania and Bulgaria. Together with Csaba Lázár, he is also responsible for the countries of Ukraine and Serbia as well as the entire area of South-East Europe.
Our supervisory board
MARTIN RATH
Expert in Laws & Rights
My vision & incentive for and with BeeWaTec
BeeWaTec is a modern and very innovative company. Since the company was founded, it has reinvented itself again and again and has driven and implemented radical product changes. Successful companies are characterised by just such a power of innovation, which is a basic prerequisite for the sustainable and successful operation of companies in today's world, where products, industries and economies are subject to rapid change.
from the vita
- Reutlingen Business High School
- University of Constance, 1st state examination in law
- Regional Court of Stuttgart, legal clerkship, 2nd state examination
- IHK Heilbronn, legal advisor
- University of Stellenbosch, South Africa, Master of Law
- 1999 - today 'Rath Rechtsanwälte'
- 2009 - today Co-Founder Apertura Sports, Athlete Management
I am pleased to be able to participate in this process through my work as Chairman of the Supervisory Board.
URS DOSCH
Expert in Management Consulting
My vision & incentive for and with BeeWaTec
BeeWaTec AG is a dynamic family business in its 2nd generation, which has more than established itself in various countries in Europe. Due to the enormous presence on the market with innovative pipe racking systems as well as constant innovations on the supply side, the company is continuously growing.
The latest technology in the field of digitalisation has also been implemented at the BeeWaTec Group. This means that the entire group communicates uniformly via the company's internal ICT technology, which makes short and fast information accessible to all country employees. And this is put into practice every day.
As part of this group of companies, I am all the more pleased to help shape the future of the BeeWaTec Group and to actively participate in it.
from the vita
- After studying economics, specialising in financial accounting, I worked as Chief Financial Officer in a holding company with various subsidiaries throughout Europe. Due to the sale of the company to the individual shareholders (management buy-out), the entire group was split into individual companies.
- This led me to my current field of activity. The fiduciary sector. First as a member of the executive board in a larger trust company. Here I acquired my knowledge in the entire field of management consultancy.
- Since 2011 I have been an independent management consultant in all areas of the fiduciary sector, be it inheritance law, commercial law, business law. I advise companies in the area of succession, restructuring and all tax law issues.
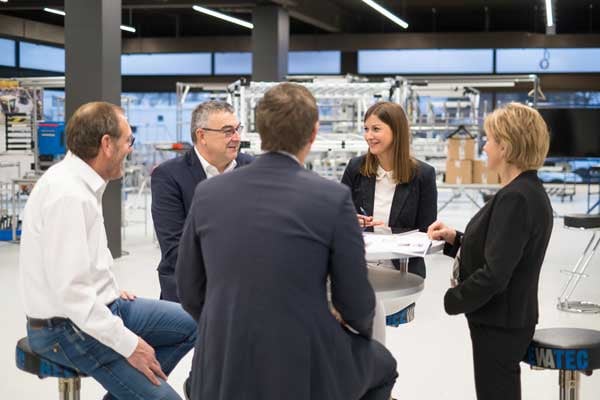
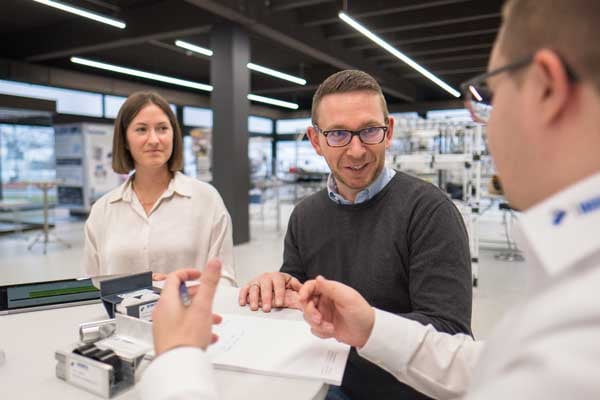
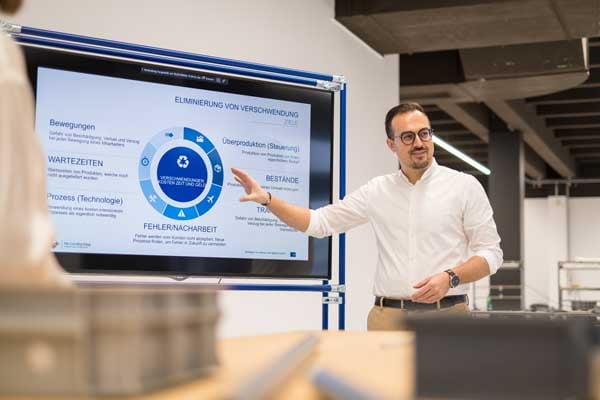
Our strategy
One of the few constants in today's world of production and work is that it’s always changing. Markets and products are subject to rapid developments, with which production and logistics must also keep pace. How successful a company is in the international competitive environment will be decided not only by the quality and prices of its products, but also by the time factor.
Launching a good idea onto the market as a product - before someone else does it; producing large quantities efficiently - at fair prices: These are the corporate goals that we at BeeWaTec consistently implement, in partnership and together with our customers, employees and sales partners.
Lean manufacturing, agile production and Industry 4.0 are buzzwords that we fill with life anew every day.
"Production and market advantages are always created when the right tool and the right material are available at exactly the right time and in the right place."
(Joachim Walter, Executive board of BeeWaTec AG)
We meet our customers where they currently are within their company development. We implement customer requirements - standardised, DIN-compliant and ISO-certified, but always as a flexible custom solution that is designed virtually and then tested and optimised in the BeeWaTec test centre under tough practical conditions. Installation, commissioning, training, technical support and ongoing development are further steps with which we consistently support our customers.
Our in-house research and development department spends a lot of time finding out what the production environment of the future will look like and what customers will want in five or ten years' time.
In terms of ergonomics, efficiency and reliable supply, we are always one step ahead of our time. Do you also want to take the lead with us?
_Web.jpg?width=600&height=400&name=Beewatec042018-(181)_Web.jpg)
_web.jpg?width=600&height=400&name=Beewatec042018-(225)_web.jpg)
_Web.jpg?width=600&height=400&name=Beewatec042018-(325)_Web.jpg)
Strong international presence
Continuous growth in stable structures - that is not only our company motto. We are globally networked and present throughout Europe.
Today, BeeWaTec and its several international subsidiaries form a powerful network for service and availability - a network that also provides our customers with a solid basis for their investments and expansion.
With our high storage capacity and precisely timed internal logistics we can guarantee just-in-time delivery. Your advantage as a customer: short delivery and realisation times as well as high product availability – turn ideas quickly and easily into functioning means of production.
We manufacture important core components in-house; this applies to electrics, mechanics, and woodworking as well as to our software modules.
Our own welding department enables smooth implementations of special adaptations.
_web.jpg?width=600&height=400&name=Beewatec042018-(16)_web.jpg)
_web.jpg?width=600&height=400&name=Beewatec-3-(54)_web.jpg)
_Web.jpg?width=600&height=400&name=Beewatec042018-(141)_Web.jpg)
The key to success:
established know-how and modern management
The basis of our company's success has always been our qualified specialist staff, whom we retain in the long term with flat hierarchies and modern corporate management. Established know-how is just as important as an early and carefully prepared generational change within top management.
This effective mix of tradition and innovation is what makes BeeWaTec so successful, both nationally and internationally - and provides your company with exactly the equipment you need to turn your ideas into reality.
_Web.jpg?width=600&height=400&name=Beewatec-3-(28)_Web.jpg)

_Web.jpg?width=600&height=400&name=Beewatec042018-(364)_Web.jpg)
Contact us.
Contact us if you have any questions, want to learn more or start your project.
Fill out this form or contact your personal sales representative in your region
directly.