Content
- What is Poka Yoke?
- Origin and development of Poka Yoke
- Poka Yoke applies to products and processes
- Advantages and disadvantages of Poka Yoke
- Top 5 areas in which Poka Yoke is used
- Examples of the application of Poka Yoke in production and logistics
- Introducing Poka Yoke in your own company in 5 steps
- Conclusion
What is Poka Yoke? Definition of the Poka Yoke principle simply explained
Poka Yoke is a principle from lean management that aims to avoid errors by designing systems in such a way that errors are either impossible or can be detected and corrected immediately. The aim is to eliminate or minimize human error sources in order to improve the quality of products or processes.
Origin and development of Poka Yoke - a principle of lean management
Poka Yoke was developed in Japan in the 1960s by Shigeo Shingo, a pioneer of lean production and quality management. While working at Toyota and other Japanese companies, Shingo recognized the need to minimize human error in production in order to improve quality and reduce costs.
The term "Poka Yoke" comes from the Japanese and means "avoid errors" or "prevent mistakes". Shingo developed this concept to create systems that are designed in such a way that errors are either impossible or can be detected and corrected immediately. His work was strongly influenced by the philosophy of lean management, which aims to minimize waste and promote continuous improvement.
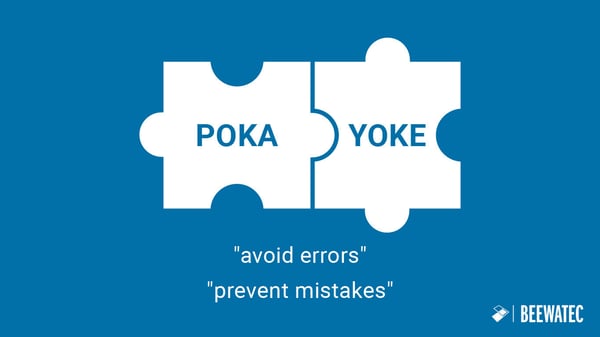
Shingo emphasized the importance of taking preventative action against mistakes rather than correcting them after the fact. Poka Yoke quickly became an integral part of lean production and was applied worldwide in various industries to improve quality, increase efficiency and reduce costs. Today, Poka Yoke is an established lean principle for error prevention and quality improvement that is used in many companies and production environments.
Avoiding errors applies to both products and processes
The principle of error prevention applies to both products and processes. Poka Yoke aims to avoid or at least minimize errors in all aspects of production.
- Products: In the context of products, Poka Yoke refers to designing products in such a way that errors are avoided during their manufacture, assembly, use or maintenance. This can be done through the use of special fixtures, labeling, color coding or other design elements that make it difficult or impossible to make mistakes.
- Processes: In terms of processes, Poka Yoke refers to avoiding errors during the production process. This means that workflows, procedures and systems are designed to minimize human error. This can be achieved by implementing checks, automated warning systems, visual instructions or other measures to detect and correct errors at an early stage.
Overall, the principle of error prevention applies equally to products and processes and is used to improve quality, increase efficiency and reduce costs.
Advantages and disadvantages of Poka Yoke
Here are the main advantages and disadvantages of Poka Yoke:
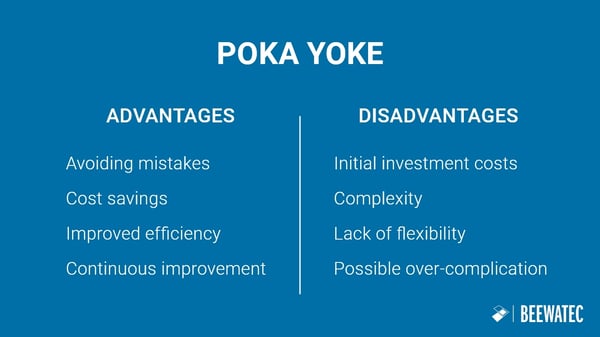
Advantages of Poka Yoke
- Avoiding mistakes: The most obvious benefit of Poka Yoke is the avoidance of errors. By eliminating or minimizing human error sources, companies can improve the quality of their products and processes.
- Cost savings: By reducing defects and scrap, companies can realize significant cost savings. Less rework, lower material consumption and fewer complaints lead to improved profitability.
- Improved efficiency: Poka Yoke helps to make production processes more efficient by avoiding unnecessary repetitions or corrections. This leads to an increase in production output and a reduction in lead times.
- Continuous improvement: Poka Yoke promotes a culture of continuous improvement by encouraging companies to analyze errors, understand their causes and take preventive measures to avoid them in the future.
Disadvantages of Poka Yoke
- Initial investment costs: The implementation of Poka Yoke solutions can involve high initial costs, especially if new equipment, training or software is required.
- Complexity: Sometimes the development and implementation of Poka Yoke solutions can be complex, especially when highly specialized production processes are involved or when customization to existing systems is required.
- Lack of flexibility: In some cases, Poka Yoke systems that are too rigid can affect the flexibility of production or work processes, especially when it comes to rapidly changing requirements or individual customer requests.
- Possible over-complication: There is a risk that Poka Yoke solutions become too complicated and production workers become overwhelmed or frustrated. In such cases, the solutions could be counterproductive and lead to delays rather than avoiding errors.
The top 5 areas in which Poka Yoke is used
Poka Yoke is used in a variety of areas in which errors must be avoided or minimized at all costs. These include:
- Production: in the manufacturing industry, Poka Yoke is often used to avoid errors in the manufacture of products. This can include the assembly of components, the processing of materials or other manufacturing processes.
- Logistics and warehousing: In logistics and warehousing environments, Poka Yoke is used to prevent errors in the picking, packing, storage and shipping of goods. This can include the use of barcode scanning systems, RFID technology or visual markers to improve accuracy and efficiency.
- Service sector: Poka Yoke can also be applied in the service sector to avoid errors in the provision of services. This can include the design of forms, processes or systems to ensure that customer requirements are correctly recorded and fulfilled.
- Healthcare: In healthcare, Poka Yoke is used to prevent errors in patient care, medication administration or patient documentation. This may include the use of checklists, double checks or other safety measures to improve patient safety.
- Software development: In software development, Poka Yoke is used to prevent errors in programming, testing and implementation of software. This can include the use of automated tests, coding standards or other quality assurance measures to detect and correct errors at an early stage.
Examples of the use of Poka Yoke in production and logistics
Here are some examples of the application of Poka Yoke in the design of operating resources such as shelving systems or workstations in production and logistics:
- Color-coded shelving: In a warehouse, shelves can be color-coded to facilitate the placement of products. By using Poka Yoke principles, employees can quickly and accurately identify and place products based on color coding, reducing the potential for errors.
- Snap-in shelf brackets: Shelf brackets can be designed to snap into place only in a specific orientation. This ensures that employees assemble the shelves correctly without errors or instability.
- Ergonomic workstation design: Ergonomic principles can be applied to the design of workstations in production to reduce employee strain and increase efficiency. For example, Poka Yoke techniques such as placing tools and materials within easy reach or using visual instructions can be used to prevent errors.
- Sensor-based monitoring systems: In logistics, sensor-based monitoring systems can be used to ensure that products or loads are stored or moved properly. These systems can detect errors, such as misplaced products or inadequately secured loads.
- Identification and labeling: The use of clear and unambiguous identification and labeling on shelves, workstations and storage facilities can help to avoid confusion and errors. This can be done, for example, by using barcode labels or visual markings that allow employees to identify products quickly and accurately.
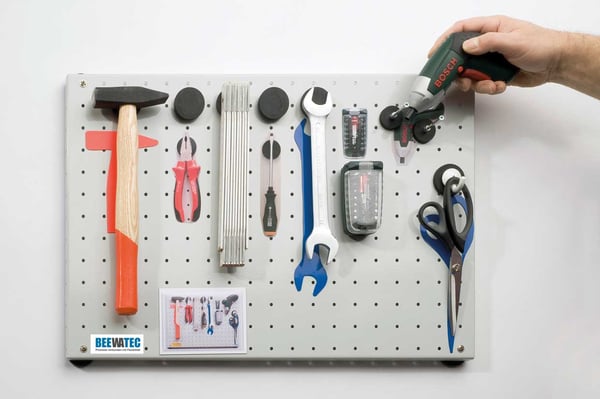
By applying Poka Yoke principles to the design of operating resources such as shelving systems or workstations, companies can increase efficiency, reduce the susceptibility to errors and improve the overall quality of their processes.
Introduce Poka Yoke in your company in 5 steps - BeeWaTec provides support
When introducing Poka Yoke in production and logistics, we recommend that companies proceed in five steps:
- Analyze existing processes and identify sources of error: Companies should first carefully analyze their production and logistics processes to identify potential sources of error. This can be done by conducting root cause analyses, error reports or employee surveys.
- Prioritization of Poka Yoke measures: Based on the analysis, companies should prioritize the identified sources of error and decide which areas would benefit the most from Poka Yoke. It can be helpful to evaluate the potential savings and improvements for each measure to support the prioritization.
- Develop and implement Poka Yoke solutions: After prioritization, companies should develop and implement specific poka-yoke solutions. This may include the design of specific tools, fixtures or work instructions to avoid or minimize human error. It is important to make the solutions simple and user-friendly to encourage their adoption by employees.
- Employee training: To ensure the effectiveness of Poka Yoke, it is important to train employees accordingly. This can include training on error detection, the correct use of poka yoke solutions and the importance of error prevention.
- Monitoring and continuous improvement: Once Poka Yoke has been implemented, it is important to regularly monitor progress and evaluate the effectiveness of the measures. Companies should seek feedback from employees to identify any weaknesses or areas for improvement. On this basis, adjustments can be made and further poka yoke measures introduced to achieve continuous improvement.
By following these five steps and systematically integrating Poka Yoke into their production and logistics processes, companies can improve quality, increase efficiency and reduce costs.
Conclusion
Overall, Poka Yoke is an extremely effective method of avoiding errors and improving the quality of products and processes. It offers numerous benefits, including the reduction of waste, cost savings and increased efficiency. By implementing Poka Yoke solutions, companies can promote a culture of continuous improvement and strengthen their competitiveness.
An important tip for getting started with Poka Yoke is to start small and take a step-by-step approach. Start by identifying areas in your company where errors occur frequently or where potential sources of error exist. Then develop simple poka-yoke solutions to avoid or minimize these errors. It is important to involve employees in the process, as they often have valuable insights and ideas on how to prevent errors. In addition, you should regularly monitor progress and solicit feedback from employees to evaluate the effectiveness of the poka-yoke measures and make adjustments as needed. By taking an iterative approach, you can gradually implement more and more advanced poka-yoke solutions and thus achieve continuous improvements in your company.